Plastic fabrication is a versatile and cost-effective process that involves manipulating plastic materials to create a wide range of products. In Australia, commercial plastic fabrication has witnessed significant growth in recent years, with numerous companies providing fabrication services to meet the diverse needs of various industries. From manufacturing and construction to automotive and packaging, plastic fabrication plays a vital role in Australia’s industrial landscape. This article explores the process of commercial plastic fabrication, the different techniques involved, and the factors to consider when choosing a fabrication service provider.
Introduction
Plastic fabrication involves the manipulation of plastic materials to create a wide variety of products, including signs, displays, packaging, and more. In Australia, the commercial plastic fabrication industry has experienced significant growth due to the versatility, durability, and cost-effectiveness of plastic. Companies providing plastic fabrication services cater to diverse industries such as manufacturing, construction, automotive, and packaging. Plastic has become an integral material in numerous applications, driving the demand for skilled fabrication services that meet industry-specific requirements.
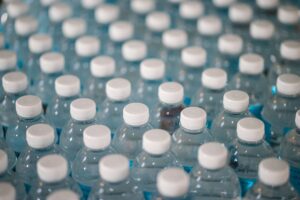
Design and Engineering
In the design and engineering phase of plastic fabrication, the fabrication company collaborates closely with the client to understand their requirements and translate them into a viable product design. This process often involves creating 2D or 3D CAD models to visualise the product and conduct feasibility studies. Designers and engineers work together to ensure that the product meets the client’s specifications while considering factors such as functionality, aesthetics, and manufacturing feasibility.
Material Selection
Choosing the appropriate plastic material is a crucial step in commercial plastic fabrication. The fabrication company considers several factors when selecting the material, including strength, durability, transparency, chemical resistance, and aesthetic appeal. Different plastic materials offer varying properties and characteristics, and the selection depends on the specific requirements of the product. The fabrication company’s expertise in material selection ensures that the final product meets the desired performance standards.
Prototyping
Before proceeding with large-scale production, a prototype, or sample, is created to verify the design and functionality of the product. Prototyping helps identify any potential issues and allows for adjustments to be made if necessary. By testing the prototype, both the fabrication company and the client can ensure that the final product will meet the desired specifications. This iterative process enhances the overall quality and functionality of the end product.
Fabrication Techniques
Commercial plastic fabrication employs a range of techniques to cut, shape, and assemble plastic materials into the desired forms. Skilled technicians and specialised equipment are utilised to ensure precise and efficient fabrication. Here are some common techniques used in commercial plastic fabrication:
CNC Machining
Computer Numerical Control (CNC) machining is a highly accurate and versatile technique used in plastic fabrication. It involves the use of computer-controlled machines to precisely cut and shape plastic materials according to the design specifications. CNC machining offers excellent precision, allowing for intricate details and complex shapes to be achieved. It is commonly used in the production of custom plastic parts, prototypes, and small to medium-sized production runs.
Plastic Welding and Bonding
Plastic welding and bonding techniques are employed to join plastic components together. Different methods, such as hot gas welding, ultrasonic welding, solvent bonding, and adhesive bonding, are used depending on the type of plastic being fabricated. These techniques create strong and durable bonds between plastic parts, ensuring structural integrity and enhancing the overall quality of the finished product.
Vacuum Forming and Thermoforming
Vacuum forming and thermoforming are techniques used to shape plastic sheets into three-dimensional forms. In vacuum forming, a heated plastic sheet is placed over a mould, and a vacuum is applied to draw the plastic tightly around the mould’s contours. Thermoforming follows a similar process but involves heating the plastic sheet and then pressing it against the mould using pressure. These techniques are commonly used in the production of plastic packaging, trays, and enclosures.
Injection Moulding
Injection moulding is a widely used technique in plastic fabrication, particularly for large-scale production runs. It involves injecting molten plastic material into a mould cavity under high pressure. Once the plastic cools and solidifies, the mould is opened, and the finished product is ejected. Injection moulding enables the production of complex shapes with high precision and repeatability. It is commonly used in industries such as automotive, electronics, and consumer goods manufacturing.
Finishing
After the fabrication process, plastic products often require additional finishing to enhance their appearance and functionality. Finishing techniques may include polishing, sanding, painting, printing, or applying protective coatings. These processes give the final product a professional and aesthetically pleasing finish, making it ready for use or display.
Quality Control
Quality control is a crucial aspect of commercial plastic fabrication. Fabrication companies implement rigorous quality control measures throughout the entire process to ensure that the final products meet the required specifications and standards. This includes inspection of raw materials, monitoring of fabrication processes, and conducting tests and measurements to verify the product’s performance and durability. Adhering to quality control practices ensures customer satisfaction and maintains the reputation of the fabrication company.
Delivery
Once the plastic fabrication process is complete, the finished products are prepared for delivery to the client. The fabrication company ensures appropriate packaging and protection to prevent damage during transportation. They collaborate with reliable logistics partners to ensure timely and secure delivery to the desired location. Efficient delivery processes contribute to customer satisfaction and facilitate the seamless integration of the fabricated plastic products into the client’s operations.
Custom Plastic Fabrication
Commercial plastic fabrication services often specialise in custom fabrication to meet specific client requirements. Whether it’s a unique product design, special dimensions, or specific functionality, custom plastic fabrication provides tailored solutions. The fabrication company works closely with the client throughout the process, from design and engineering to final production, ensuring that the end product meets their exact specifications.
Plastic Sheet and Rod Cutting
In addition to fabrication, many plastic fabrication companies offer plastic sheet and rod cutting services. Using precise cutting equipment, they can cut plastic sheets and rods to the desired dimensions. This service is particularly useful for clients who require specific sizes of plastic materials for their own fabrication processes or projects.
Conclusion
Commercial plastic fabrication encompasses a wide range of processes and techniques to transform raw plastic materials into functional and aesthetically appealing products. With the advancement of technology and the expertise of skilled technicians, plastic fabrication continues to evolve, enabling the production of complex and customised plastic components. Whether it’s CNC machining, plastic welding, vacuum forming, or injection moulding, these techniques contribute to the manufacturing of high-quality plastic products that find applications in various industries.
You may also like: