PLEXIGLAS® is a break-resistant safety glazing material of supreme weather resistance. We guarantee that clear, transparent PLEXIGLAS® will show no yellowing and will retain a high level of light transmission for 30 years. It is highly light-transmitting (92 % in Clear at 3 mm thickness). The IR-reflecting material PLEXIGLAS HEATSTOP® XT offers advantages of quite a different nature; used for domed or continuous roof lights, it lets in daylight whilst reducing undesired heat buildup indoors. PLEXIGLAS® is very light in weight; a sheet 3 mm thick and measuring one-meter square weighs only just 3.6 kg. PLEXIGLAS® can be cold-curved, but certain minimum radii have to be observed.
A particularly break-resistant material during handling, fabricating, installation and in use is impact-modified
PLEXIGLAS RESIST®.
Natural protection against yellowing and light loss. Together with light and warmth, the sun also emits UV radiation. The dangerous portion of this UV light that reaches the earth is growing as a result of the hole in the ozone layer. PLEXIGLAS® consists of extremely strong, UV-stable molecular chains through and through. Special NATURALLY UV-STABLE technology stabilizes PLEXIGLAS® completely from within. This means the entire sheet is protected, not just the surface, providing maximum protection against UV radiation, yellowing and light loss.
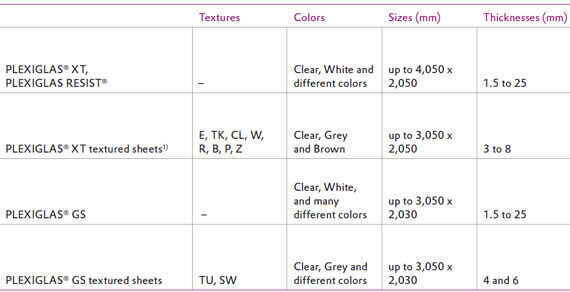
Design Hints
(a) Changes in length and allowance for expansion



PLEXIGLAS® sheets expand due to heat and/or moisture and contract in a cold and/or dry climate. Therefore, the fastening systems must be able to yield, so as to allow the sheets to move. The sheet lengths are to be measured in such a way that the sheets cannot slip out of the glazing sections when they are cold. On the other hand, the material must be able to expand unhindered when it is warm in order to rule out damage due to buckling, for example. Assuming an ambient temperature of 10 °C on installation, the sheets will contract up to 2.5 mm per metre in the cold (Fig. 1). For their expansion due to heat and moisture, a general allowance should be made of
5 mm/m for PLEXIGLAS® (*),
which is the distance to the “clear cross-section” of the frame. Because of the possible change in length, the clamping depth of the glazing should be between 15 and 20 mm. In addition, there is to be a clearance “a” for expansion and compensation for building tolerance. The value “a” depends on the sheet size and corresponds to one half of the general expansion allowance calculated as above (Fig. 2 and 3).
(*) In comparison with basic grades of PLEXIGLAS®, PLEXIGLAS RESIST® sheets, as a result of their increased break resistance, are less rigid and more
prone to expand in heat and moisture:
6 mm/m for PLEXIGLAS RESIST® 65 and 75,
8 mm/m for PLEXIGLAS RESIST® 100
(b) Sealing sections and corner joints


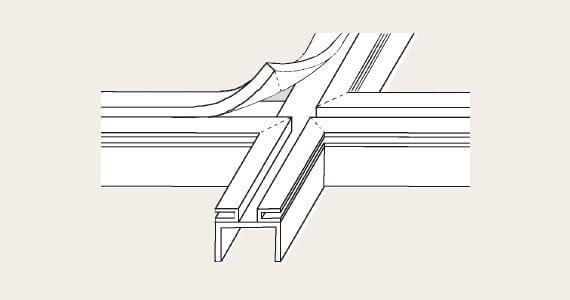

The sealing sections used to determine the water tightness of glazing with PLEXIGLAS®. Particularly important is the material they are made of.
PLEXIGLAS® is sensitive to certain sealants, which should therefore always be tested for compatibility.
Normally suitable:
- EPDM
- polychloroprene
- PE, PTFE, PA
- silicone rubber
Nearly always harmful:
- plasticized PVC
- polysulphides
- PUR foams
The sealing sections must be able to balance the changes in the length of PLEXIGLAS® and have to be designed accordingly. They have to be mechanically secured against slipping out. Bonding is not
enough (Fig. 4)!
The sheets can be additionally sealed with compatible silicone (e.g. KÖDISIL® HAC, SILPRUF‚ or the like) where this is required or where a gasket is to be held in place. In this case, the sheets should not exceed “door panel size”.
Corner joints of the seals
Joints and corners of the seals frequently constitute the weak points of glazing in terms of water tightness. Depending on the requirements, the joints should be designed as follows:
- continuous vertical seals with recesses and overlapping horizontal seals which drain into the vertical ones (Fig. 5)
- welded or corner-vulcanized seals (Fig. 6)
- preformed corner sections mmouldedon to straight sections (Fig. 7)
(c) Fastening methods

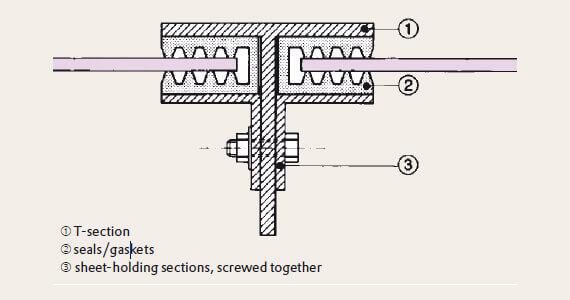

Structural components made of PLEXIGLAS® can be fastened pointwise or linearly.
Pointwise fastening is suitable for
- small glazing areas,
- irregularly curved glazing,
- inherently stable items, e.g. domed roof lights or thick sheets.
Fig. 32 and 33 show drill holes and screwed connections designed for use with PLEXIGLAS®.
As a general principle, linear fastening is to be preferred since the load conditions are more favourable in this case and thinner sheets can be used as a result. The allowance to be made for expansion is again 5 mm/m for PLEXIGLAS® (PLEXIGLAS RESIST® 6 resp. 8 mm/m).
The linear fastening method is particularly suitable for
- large glazing areas,
- regularly curved glazing,
- cold-curved glazing elements
In the case of linear fastening, the change in length is balanced by the sheets sliding in between the seals or by flexing of the seals. This edge fastening system has to be watertight without being so rigid as to prevent the sheets from moving. Linear fastening has the advantage that the forces resulting from the loads (dead weight, wind, snow) are evenly distributed over the supports. The figures (Fig. 8 to 10) show further details and examples of linear fastening.
(d) Contact pressure
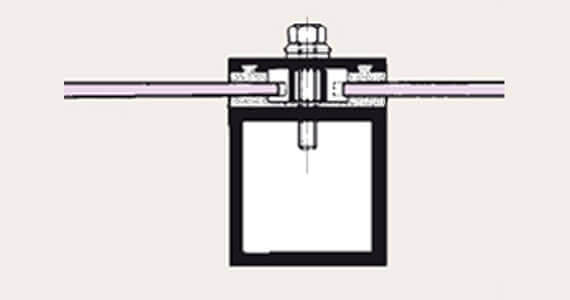




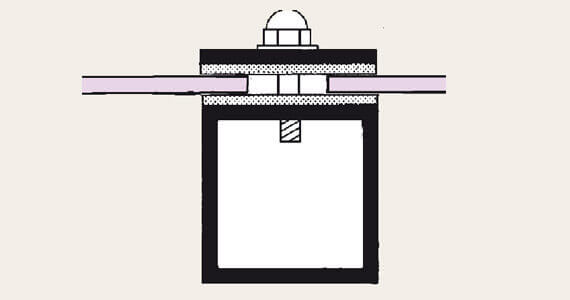


An important aspect with all constructions is the contact pressure, i.e. the force produced by the screw and transmitted to the elastic sealant via the fastening elements.
This pressure must be calculated in such a way that adequate tightness is achieved while the sheets can still slide in response to linear thermal expansion (Fig. 11). If the contact pressure is too high, this may be detrimental to the system. Since the pressure affects above all the weakest link in the fastening system, the elastic seal becomes excessively compressed, whereupon the clamped PLEXIGLAS® sheets can no longer move properly. Depending on the construction and the materials and sealants used for the fastening system, upsetting deformation and buckling occur or the seals are displaced. Thus it may happen that the movement of the sheets causes the seals to slip out of the frames and lose their tightening function (Fig. 12). Apart from that, excessively compressed seals quickly lose their elasticity and thereby also their sealing function (cf. (b) “Sealing sections”).
The structural means shown schematically can be recommended for regulating the contact pressure (Fig. 13 to 18).
(e) Types of glazing




Single glazing
Applications
Windows, doors and indoor partitions
- Guards
- Overhead glazing outdoors
- Noise-control barriers
- Safety glazing
- Sight screens.
Single glazing is above all used in areas where protection against the weather is required, but no heat insulation (Fig. 19).
Double and multiple glazing
Double and multiple glazing is installed to satisfy special requirements in terms of heat or sound insulation (Fig. 20 to 22).
Thin sheets of PLEXIGLAS® can be formed with ease. Adequate stability can be achieved by the uniaxial (usually cold) or biaxial (always warm) curving of the sheets. Bending of the sheet edge to a right angle provides extra stability so that even large areas can be double- or multiple-glazed. Therefore multiple glazing of PLEXIGLAS® is particularly suitable for constructions which are designed to be curved (domes, barrel vaults, cones, etc.)
Joining of sheets
The individual sheets are glued to strips of PLEXIGLAS® or light metal sections at the edges, e.g. using compatible double-sided adhesive tape (Fig. 22), or else they are clamped directly as shown
in Fig. 20 and 21.
Since PLEXIGLAS® is somewhat permeable to water vapour, double or multiple glazing has to be vented towards the outside, so as to rule out condensate formation as for as possible or else to expel the moisture again. The same applies to rebates. At the lower end of the glazing, holes must be provided for venting and drainage: detail A in the figure shows a longitudinal section through the front end of a double-layer barrel vault (Fig. 22).
(f) Standard details
Our pictures show typical examples of assembly details which suit the special character of PLEXIGLAS® sheets (principles only, not product recommendations).


- Contact pressure regulated via spacer sleeve over the threaded rod
- Spacer sleeve also protects sheet edges against the sharp thread
- Weather seal with a sloping face protects against stagnant water
- Condense drainage via spacer strip
- Baffle plate all across glazing bar guides water

- Contact pressure regulated via threaded rod and cap nut
- Allow enough room for expansion at the sheet

- Contact pressure regulated via the limited thread of a threaded rod plus cap nut
- Threaded rod penetrates shim
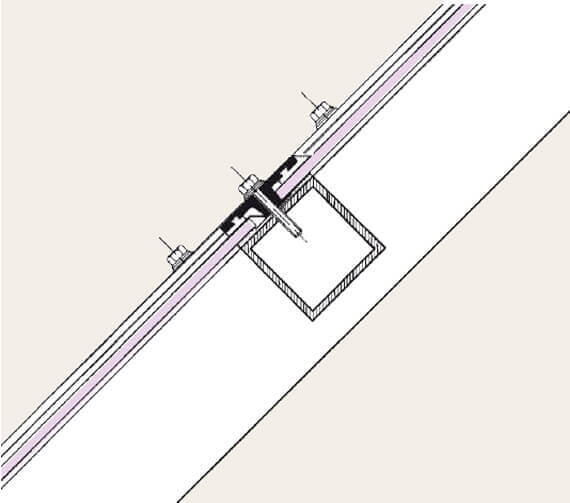
- Contact pressure regulated via projecting screw channel
- Seal with sloping face protects against stagnant water
- Baffle plate to guide water extends over second sealing plane
- Allow adequate room for expansion at the sheet
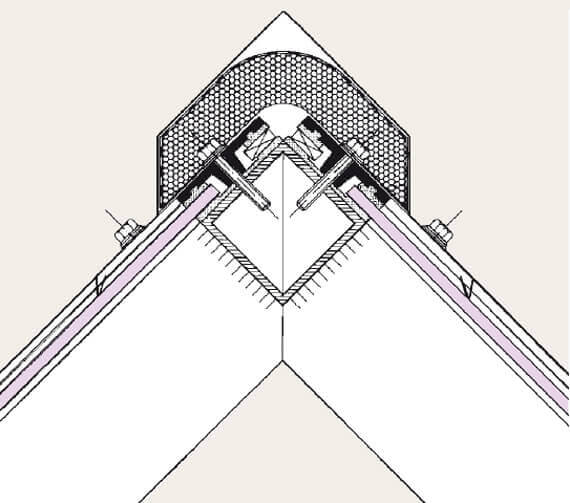
- Contact pressure regulated via projecting screw channel
- No cold bridges because of insulation
- Allow enough room for expansion of the sheet

- Contact pressure determined by threaded rod and cap nut
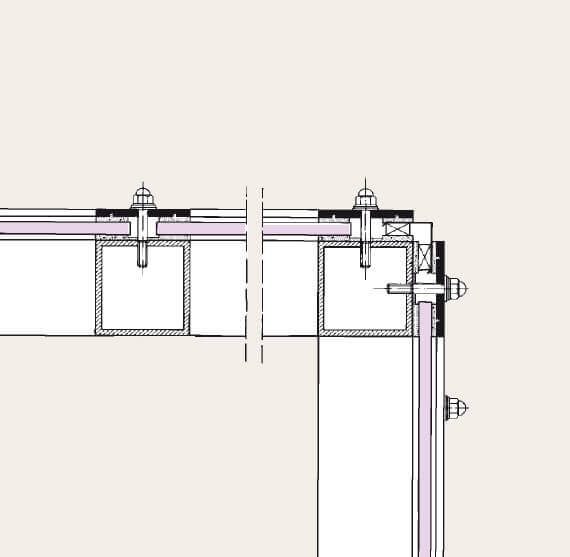
- Contact pressure determined by threaded rod and cap nut
- Angle section covers the corner
Applications
The details described so far open up a wide variety of applications. PLEXIGLAS® sheets are the materials of choice wherever windows, doors, gates, guards and roofs call for break-resistant to unbreakable or lightweight glazing.
PLEXIGLAS® GS resp. XT e.g. for heat-insulating secondary window glazing in private houses and public buildings, factory units and sports halls; for break-resistant glazing in curtain walls and glazed openings for industrial, commercial and agricultural use, within sports complexes (safety glazing for ice hockey rinks from 12 mm in PLEXIGLAS® XT and 6 mm in PLEXIGLAS RESIST® 65, -75 and -100) and for dance floors.
PLEXIGLAS RESIST® e.g. as secondary glazing in private houses, public buildings, factory units and sports halls, schools, kindergartens, bus shelters; as anti-burglar glazing in shop windows of jewellers, furriers, carpet and gun dealers; as a safeguard against vandalism and terrorist attack.
PLEXIGLAS® XT textured sheets are particularly suitable for applications which require transparency to light but not to the view, e.g. in balcony guards, staircase balustrades, door panels and partitions.
On the special requirements to be met by our glazing materials, “UV protection” and “Protection against attack”, follow two separated remarks.
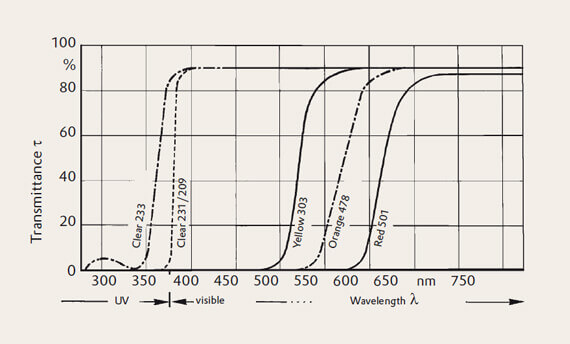
UV protection
If light-sensitive exhibits like paintings, drawings, prints, stamps, textiles, leather etc. are exposed to daylight, they may be permanently harmed by fading, yellowing or embrittlement. Since the short-wave, ultraviolet portion of the illuminating radiation is primarily responsible for these effects, replacement or secondary glazing with a UV-filter effect – instead of or additionally to conventional mineral glazing with a permeability of about 15 % – serves a protective function here.
On the other hand, however, the wavelength of 380 nanometers which is regarded as the end of the ultraviolet range does not constitute a sharply defined boundary between photochemical attack and safety of the irradiated material, so that filter glazing whose permeability begins at longer wavelengths in the visible range affords much better protection. Such glazing sheets are then no longer clear-transparent but of a yellowish-orange colour. The table presents a few PLEXIGLAS® grades whose UV permeability is particularly low.
Owing to their reflex-scattering effect, sheets of PLEXIGLAS Gallery® AR (= antireflective) are used for picture glazing with the picture directly behind. A figure illustrates the increased protection afforded by some transparently coloured PLEXIGLAS® GS grades (Fig. 23).

Protection against attack (“safety glazing”)
Glazing protecting against attack has been standardised to DIN 52 290 1); procedures are running for standardisation throughout Europe. It is defined as a translucent or transparent material based on glass or plastics, single- or multilayer, which offers resistance to violent attack.
The different types of attack and the corresponding resistance classes are described in parts 2 to 5 of this standard. Table 1 shows which of our semi-finished products have been successfully tested for certain resistance classes:
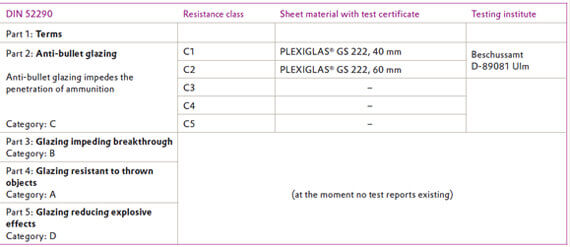
Conclusion: PLEXIGLAS® GS Clear 231 or PLEXIGLAS Gallery® Clear 21570 AR to afford very good protection against UV radiation, whereas PLEXIGLAS® GS Yellow 303 is completely UV-absorbing.
(a) Flat roof and vertical glazing
The required thickness of PLEXIGLAS® sheets depends on
- the envisaged use
- the rebate depth (= clamping depth plus a half allowance for expansion; see “(a) Changes in length and allowance for expansion”)
- the sheet size
- the snow and wind loads to be assumed for a given
location (e.g. to DIN 1055).


For flat sheets that are clamped all around, the thickness can be taken from Tables 2a and b. To this end look at Table 2a first and read the area factor
(letter) corresponding to the given length and width.
Together with the load, this leads to the recommended thickness in Table 2b.
The upper value applies to PLEXIGLAS®, the lower one to PLEXIGLAS RESIST® 65. In this case, a deflection of 1/50 of the sheet width (= 2 %) – a permissible value for plastics – is not exceeded, so that aesthetic appearance and economy are guaranteed.
Moreover, the recommended thicknesses are calculated so as not exceed the maximum permissible material stress of 10 MPa at the given load.
The data are based on calculations, experimental results and long-term experience.
Where written proof is required in individual cases, a structural engineer has to be entrusted with the static calculation.
Example: A roof with an expected snow load of 750 N/m2 is to be glazed with sheets 3 m long and 0.75 m wide. According to Table 2a, these dimensions lead to an area factor G which together with the load in Table 2b shows this result: 6 mm thickness for PLEXIGLAS® GS / XT or 8 mm for PLEXIGLAS RESIST® 65.
Exceptions:
- If the sheets are clamped at the long sides only, the second next highest sheet thickness according to Table 2b should be used, e.g. 8 mm instead of 5 mm, 15 mm instead of 10 mm etc., to be on the safe side.
- Where the main reason for choosing for PLEXIGLAS RESIST® is protection against vandalism, and as long as increased deflection is no problem, the sheet thickness according to Table 2b can be fallen short of if the rebate depths are increased at the same time (see “Secondary glazing”).
(b) Secondary glazing
Secondary glazing means glazing installed in front of or behind the existing wall, door and window glazing. Although it also serves for heat and sound insulation, its main purpose is usually to protect against damage caused by unruly children and youngsters, carelessness, shock, stones thrown against it, acts of vandalism etc. (see also “Protection against attack”). Since this calls for a very impact-resistant material, we recommend PLEXIGLAS RESIST®.
Against break-ins:
- A second glazing sheet of PLEXIGLAS RESIST® on the inside of the existing glazing: The burglar, having damaged the glass pane, is confronted with impact-resistant PLEXIGLAS RESIST® which offers remarkable resistance against his standard tools.
Against aggression, vandalism and terrorism:
- A second outer pane of PLEXIGLAS RESIST® affords superior protection against hurled objects or impact stress of windows in private and public buildings and churches, for example The impact resistant PLEXIGLAS RESIST® sheet wards off things thrown or hit against it and prevents the glass behind it from breaking.
Normally a rebate depth of 25 mm is adequate for this purpose.
Given substantial rebate depths, or if the sheets are additionally secured by screwed connection with the frame, the thickness according to Tables 2a/b may be reduced. Since glazing installed mainly to ward off attacks may yield more strongly than “ordinary” window glazing, the thickness of the PLEXIGLAS RESIST® sheets can remain one or two steps below the tabulated value (e.g. 6 or 5 mm instead of 8 mm).
PLEXIGLAS RESIST® sheets that are installed in front of existing glazing should be spaced at about 60 to 70 mm in order to be able to flex freely after an impact without damaging the glass. This applies to PLEXIGLAS RESIST® sheets of size 2,000 x 1,200 mm and 8 mm thick, for example.
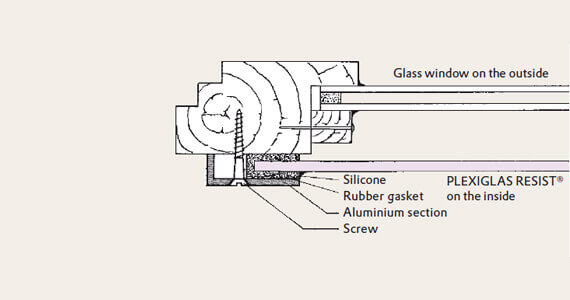
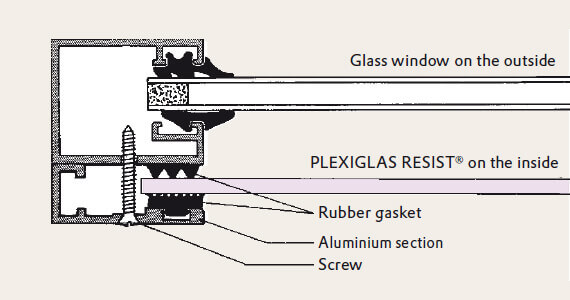

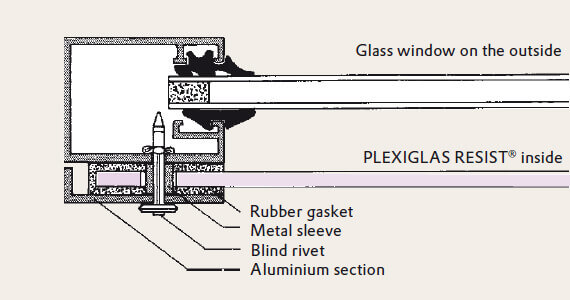
When cutting the sheets to size it must be borne in mind that PLEXIGLAS RESIST® needs an allowance for expansion of c. 6 mm per meter of edge length.
PLEXIGLAS RESIST® sheets are to be provided with an all-around rubber seal, inserted in a clamping frame and then screwed to the door or window frame or anchored in the masonry.
When selecting the seal, care must be taken that it is compatible with PLEXIGLAS RESIST®, which is true of EPDM, for example. The clamping sections used with the PLEXIGLAS RESIST® sheets must be stable enough to resist shock and impact without separating from the existing frames or releasing the sheets. Apart from the clamping sections specially designed for use with PLEXIGLAS RESIST®, commercially available angle sections similar to those shown in the figures can be used (Fig. 24 to 27).
(c) Barrel vaults roof glazing
The barrel vault roofs frequently used in modern architecture are inconceivable without plastics such as PLEXIGLAS®. Since ease of shaping is one of their typical properties, flat sheets can be cold-curved on site (thermoformed items are rarely used for this purpose) over a correspondingly arched supporting structure.

These are the benefits of barrel vaults:
- high loadbearing capacity if curved sheets are clamped all around,
- aesthetic appearance with high light transmission and transparency
- adaptation to virtually any building style
- cost saving due to cold curving.
Cold curving can only occur uniaxially. Pyramids, cupolas and the like have to be thermoformed. Uniaxial curving is feasible in different cross-sectional configurations, which have advantages and disadvantages, however. The compromise most often used in practice is barrel vaults in the form of circular arcs with a uniform curving radius.

The figure shows the structural principle of a barrel vault. On the supporting structure, the cut-to-size sheets are cold-curved over correspondingly farmed (metal) hoops and fastened with clamping bars (e.g. screwed down between the sheets) over the length of the arch. The same system is used to fasten the lower ends to the gutter sections. Compatible seals are used in between clamping system and sheet (Fig. 29). Otherwise, see “Design hints”.Cold curving generates stress within the material which has to be limited. Therefore it is essential to observe the minimum cold-bending radius (r min) specified for a given sheet thickness. The radii applicable to our materials are given in Table 3 or can be calculated according to the equation described below.

In order to design a barrel vault with PLEXIGLAS® one needs to know at least
- the bending radius (r):
if unknown, it can be calculated from the pitch (h) and span (s) according to this equation: - the arc length (b),
which can be calculated as follows:
r=( h/2 ) + ( s^2/(8 . h))
b≈√((s^2 + 16/3*h^2)) - the hoop spacing,
i.e. the approximate width of the individual cut-to-size sheets for the vault which, for reasons of material technology, should not be larger than max. 1,500 mm for all PLEXIGLAS® sheets.
Once the designer has specified these dimensions, or they have been established on site, or calculated as indicated above, the sheet sizes can be determined to take the following into account:
- the available sizes according to our sales range brochure or as inquired of the stockist, in order to produce a minimum of costly waste;
- the necessary clearance for material expansion.
In the case of barrel vaults with greater arc lengths than the available sheet lengths, the arc has to be divided up (at the ridge or several times) by putting several sheets together with transverse joints. The same clamping systems as for the curved hoops are to be used for the transverse joints and due allowance is to be made for expansion.
The required sheet thickness can be taken from Table 4a or 4b. The values were calculated with a safety factor of 1.5 against buckling, according to E. R. Berger: “Art approximation formula for the buckling stress on a concentrically compressed arched shell,” Beton- und Stahlbau 48 (1953), p. 288. These data are meant as a guideline for our customers. Where proof is required, entrust an engineer with the static calculation.
Example: For a barrel vault with a snow load of 750 N/m2 and a hoop spacing of 1,000 mm at a radius of 3,000 mm, use 5 mm thick PLEXIGLAS® or 6 mm thick PLEXIGLAS RESIST® 65.
above PLEXIGLAS® GS and XT, below all grades of PLEXIGLAS RESIST® 65
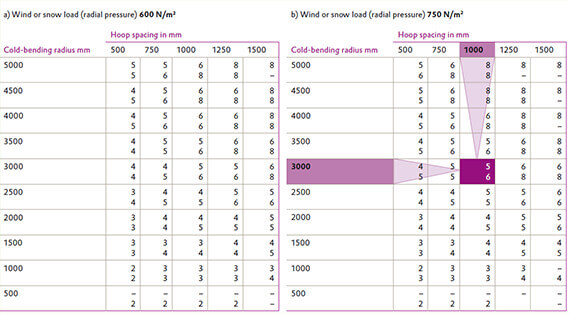
(d) Infill panels for balcony guards and staircase balustrades
Being available in many different colours and thickness, sheets of PLEXIGLAS® GS and XT are often used as infill panels for balcony guards and balustrades. PLEXIGLAS® XT sheets are, moreover, popular for their ten surface textures in thickness up to 8 mm.
PLEXIGLAS RESIST® sheets are installed where extreme impact strength is required in addition to safety for the users.
- Despite this advantage, we recommend choosing somewhat thicker infill panels made of PLEXIGLAS RESIST® than of PLEXIGLAS®, so as to make up for the reduced stiffness of the impact-resistant material.
- The sheet thicknesses recommended hereafter were determined in a pendulum impact test, striking the infill panel mounted in a sturdy frame with a sandbag. The frame has a major influence on the stability of the structure; hence the need to have it tested under standard conditions by a competent institute.
- Balcony guards and staircase balustrades are subject to building inspectorate regulations, which have to be observed. A balcony infill panel, for example, must be at least 900 mm high.
- Grades of PLEXIGLAS® are “normally flammable”, B 2 to DIN 4102 (Class 3 and TP(b) to British Standards) and as such approved in Germany for use in balcony guards on buildings up to two storeys high.
- PLEXIGLAS® XT sheets with one textured surface are best installed with the texture facing inwards; on the one hand, because of the visual effect and on the other hand to make good use of the self-cleaning effect by rain on the outside.
(1) Clamping all around
- Many users choose standard metal sections for clamping the sheets (Fig. 30). This is possible with PLEXIGLAS® as long as the due allowance is made for the change in length and only sealants compatible with PMMA are used.
- Commercially available installation kits as shown in figure “Clamping on two sides” are also suitable
- The lower channel sections should be provided with drain holes.
- At a maximum sheet length of 1,500 mm and a height of not more than 800 mm, the minimum required sheet thickness is 6 mm and the minimum rebate depth for the channel sections 20 mm.
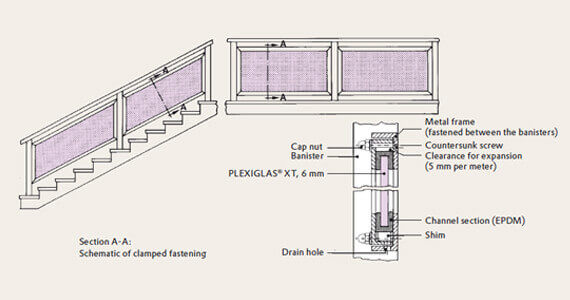
(2) Clamping on two sides
- As regards expansion, sealing, sheet size etc., the recommendations are the same as under (1).
- Given a maximum sheet length of 1,500 mm, for example, and a maximum height of 800 mm, the required sheet thickness is 8 mm and the rebate depth of the clamping sections at least 20 mm.
- Cut sheet edges that remain visible should be smoothed with a scraper or chamfered with a file.

(3) Fastening at Bannisters
- If the sheets are to be installed between bannisters without any further support, the necessary stiffness must be ensured by using sheets of adequate thickness between reasonably spaced bannisters.
Thus, if the bannister spacing exceeds 1.2 m, thicker sheets (outside the textured sheet range) have to be used, PLEXIGLAS® XT and PLEXIGLAS® GS sheets are available in thickness of up to 25 mm.
- Since the screwed connection of acrylic is only the second-best installation method (after clamping), care must be taken to proceed according to the figure.
- Drill holes must be much larger in diameter than the screw thread.
- Protect the sheet wall inside the drill hole with a compatible sleeve (e.g. polyethene) around the thread.
- Use large washers with the screws and compatible elastic seals (e.g. EPDM).
- Tighten the screws only to such an extent that the sheets are still able to move.

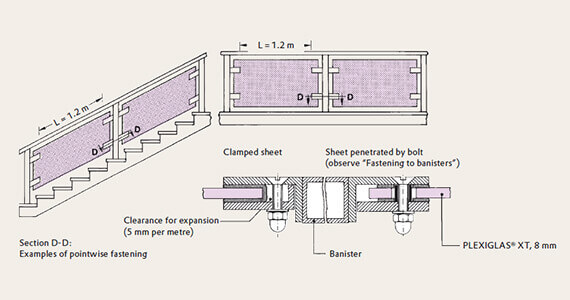
(4) Pointwise fastening
- Where metal tongues are used, the sheets are held in position by bolts and nuts, which either clamp or penetrate them according to the figure.
- Since the sheet will transmit the generated stress irregularly to the supporting balustrade, it is essential to observe every single detail mentioned under “Fastening to bannisters” (text and figure).
- This solution is particularly elegant if the sheet edges are polished.
(e) Walkable floor glazing
The floors or ceilings of buildings and the floors of balconies which would otherwise cast shadows are sometimes glazed to transmit light, and this glazing must then be walkable. Dance floors, too, are frequently provided with transparent and/or illuminated glazing. PLEXIGLAS® GS sheets or blocks are optimally suited for this purpose, because,
- they are seven times as break-resistant as glass,
- show outstanding resistance to ageing,
- are available in much different load-bearing thickness and
- come in a wide variety of surface textures and colours.
Such floors must be rigid and by no means resilient. What applies, in general, is that the total surface area has to be divided up into individual elements of reasonable size, a structural engineer has to be entrusted with the calculation of the load bearing substructure as a grid of longitudinal and transverse members. The regional building and fire regulations are to be observed. According to DIN 1055, ceilings, for example, have to be designed for a traffic load of 5,000 N/m2, in which case the thickness according to Table 5 is recommended (sheets and blocks of PLEXIGLAS® GS cut to size without any waste):
Fire behaviour / Cleaning and care
The natural wear occurring when acrylic is walked or driven over can usually be tolerated for such floors, otherwise, the scratches can be made invisible by previous dull-grinding (e.g. using an orbital sander and wet abrasive paper). Alternatively, the PLEXIGLAS® GS sheets/blocks can be covered with textured sheets of PLEXIGLAS® XT (e.g. using ACRIFIX® 190 / CATALYST 20 for bonding) over their entire surface area. Scratches become invisible, the slip resistance is improved and the floor can no longer be seen through while remaining light-transmitting.
In the rebates of the supporting grid, which should be about 15 to 25 mm deep, the PLEXIGLAS® GS elements should rest on PMMA-compatible EPDM or polyethene strips.
For outdoor applications, in particular, PMMA-compatible silicone seals, for example, are to be inserted in the expansion joints between the glazing elements and their frames.
Fire Behaviour
- PLEXIGLAS® is rated in Euroclass E to DIN EN 13501 with regard to fire behaviour.
- PLEXIGLAS® burns almost without smoke according to DIN 4102 and is easy to extinguish.
- The smoke gases produced by PLEXIGLAS® are not acutely toxic according to DIN 53436 and are non-corrosive according to DIN VDE 0482-267.
- Roof surfaces glazed with PLEXIGLAS® open up by melting in the event of a fire and allow smoke and heat to escape.
Cleaning and care
- Given adequate roof pitch or vertical glazing in residential areas, cleaning on the outside is not required. Dirt is normally washed off by the rain, otherwise hosing down is enough.
- PLEXIGLAS® sheets have smooth surfaces to which dirt cannot adhere. Dust is removed with water to which some dishwashing liquid has been added and with a soft cloth or sponge. Never wipe the material dry and do not use a scouring agent. For thorough cleaning, use ANTISTATIC CLEANING AGENT (Burnus GmbH, Darmstadt), obtainable from your stockist.
- In the case of subsequently installed secondary glazing, the gap between the existing glazing and the PLEXIGLAS® sheets has to be cleaned moist and then dried before it is finally sealed.
- Should there be an unsightly scratch on a sheet of PLEXIGLAS® a rarity with textured sheets this can be removed with ease? Rough grind the scratched area wet with waterproof sandpaper of, say, grit 240 and fine-grind with grit 400 to 600. Then polish with a soft cloth or buffing wheel, using ACRYLIC POLISHING PASTE (by Burnus) or a commercial car polish.
- Large glazing areas or facades are often cleaned mechanically. None of these methods whether rotating brushes, squeegees or the like – are suitable for PLEXIGLAS®. Even if copious amounts of water are used, the risk of scratching the sheet surfaces cannot be excluded. Commercially available high-pressure hot-water cleaning units, on the other hand, are most suitable. We recommend adjusting the pressure to between 50 and 100 bar and the water temperature to between 50 and 80 °C. Add a small quantity of a moderately foaming cleaner concentrate to the wash water via the integrated dosing unit, e.g. BURLANA® by Burnus. Subsequent wiping down is neither necessary nor advisable since the sheet surface dries well enough in the air.
For Enquiries, Please don’t hesitate to CONTACT US.